材質変更で、コストダウン&長寿命を実現!
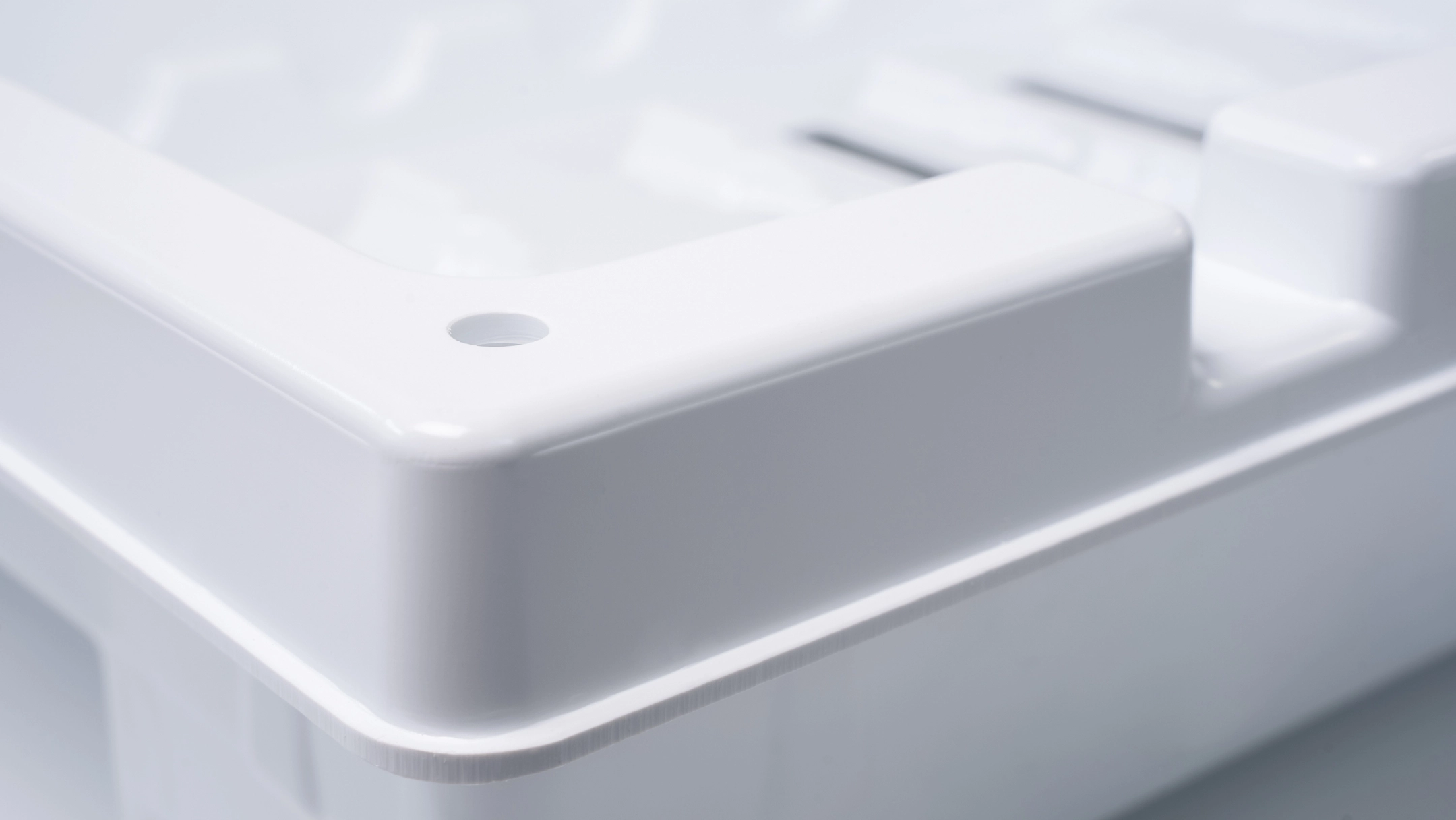
お客様の課題・リクエスト
自動車部品を収納する箱を作りたい。現状、ABS樹脂を使用しているが、割れてしまう問題がある。形状を変更して解決できないか?
ご提案
割れてしまった実物をお送りいただき、調査しました。お客様は形状変更が必要だと考えていましたが、調査の結果、ABS樹脂自体に原因があることが判明しました。
ABS樹脂は耐衝撃性に優れているものの、油に弱いという特性があります。お客様の現場では重い材料を扱い、油も使用しているため、ABS樹脂は適していませんでした。そこで、形状変更ではなく、材質を耐衝撃性と耐薬品性に優れた塩ビ材に変更することをご提案しました。
結果・成果
工法を変更せずに材質だけを変えたため、型費用が発生しませんでした。また、割れないため長寿命化を実現し、耐久性が約150%向上しました。長期的にはコストダウンにも大きく貢献した事例です。
射出成形から真空成形への工法転換で、
イニシャルコストを削減
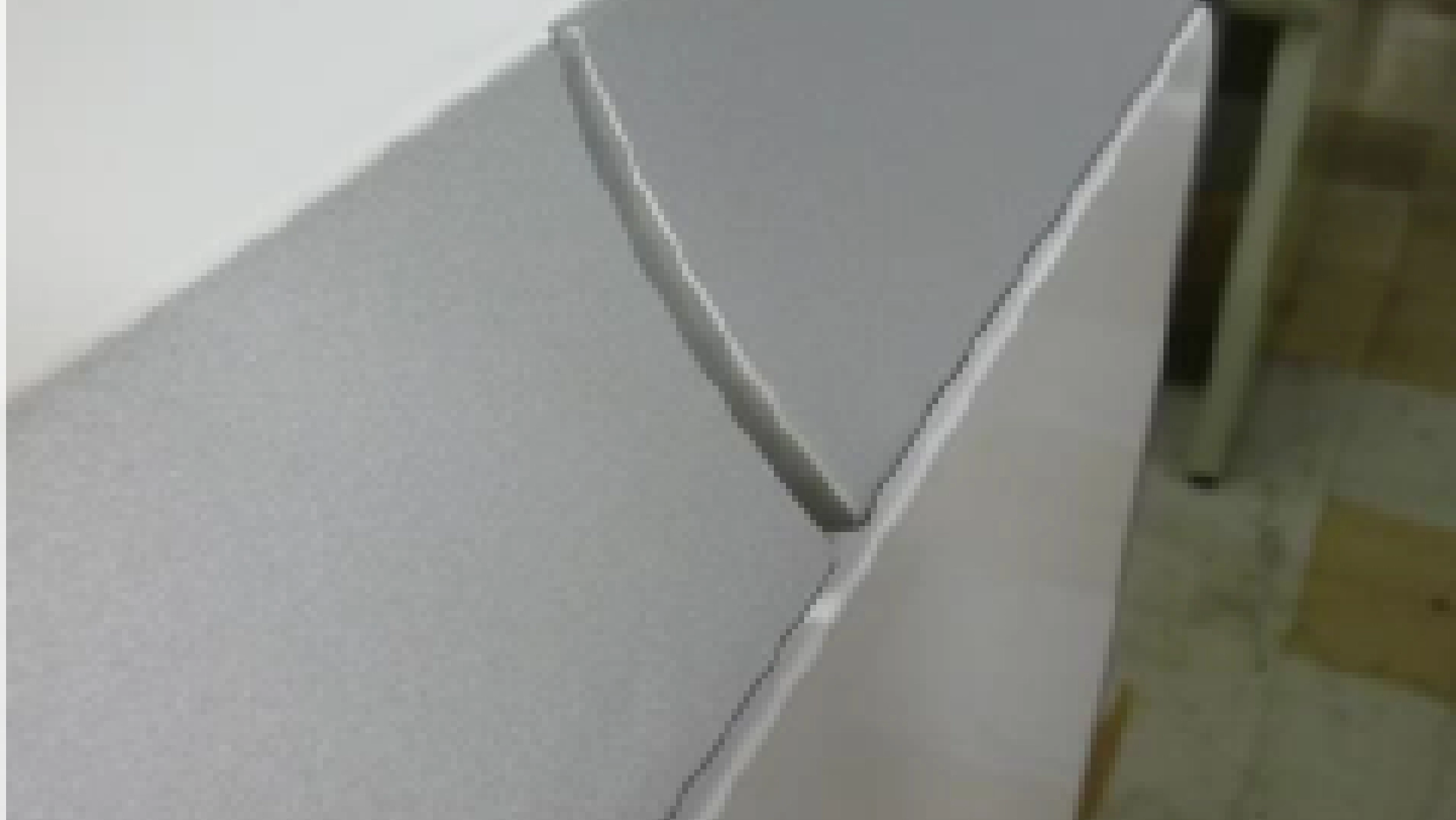
お客様の課題・リクエスト
新製品として分析装置を手掛けているが、インジェクション成形(射出成形)では型のイニシャルコストが約7,000万円かかる。何かコストを抑える方法はないか?
ご提案
事情をお聞きしたところ、年間の需要は40台という生産台数が少ない製品でした。
そこで、真空成形の技術をご説明し、射出成形から真空成形に工法を変更しました。
真空成形では射出成形と同等の精度を出すことが難しいため、寸法に関して設計の見直しが必要でした。お客様と三次元データのやり取りをしながら設計変更を行い、試作型を作って確認しながら製作を進めました。
結果・成果
型の製作期間を約1/3に短縮し、試作提供までの期間が1ヶ月で済みました。
さらに、イニシャルコストを約1/10に抑えることができ、製品単価も低減しました。具体的には、7,000万円の金型費が500万円で済んだ事例です。当社では新製品の開発段階から、コスト削減に向けたご相談に対応しています。
図面がない…ポンチ絵だけで製作できますか?
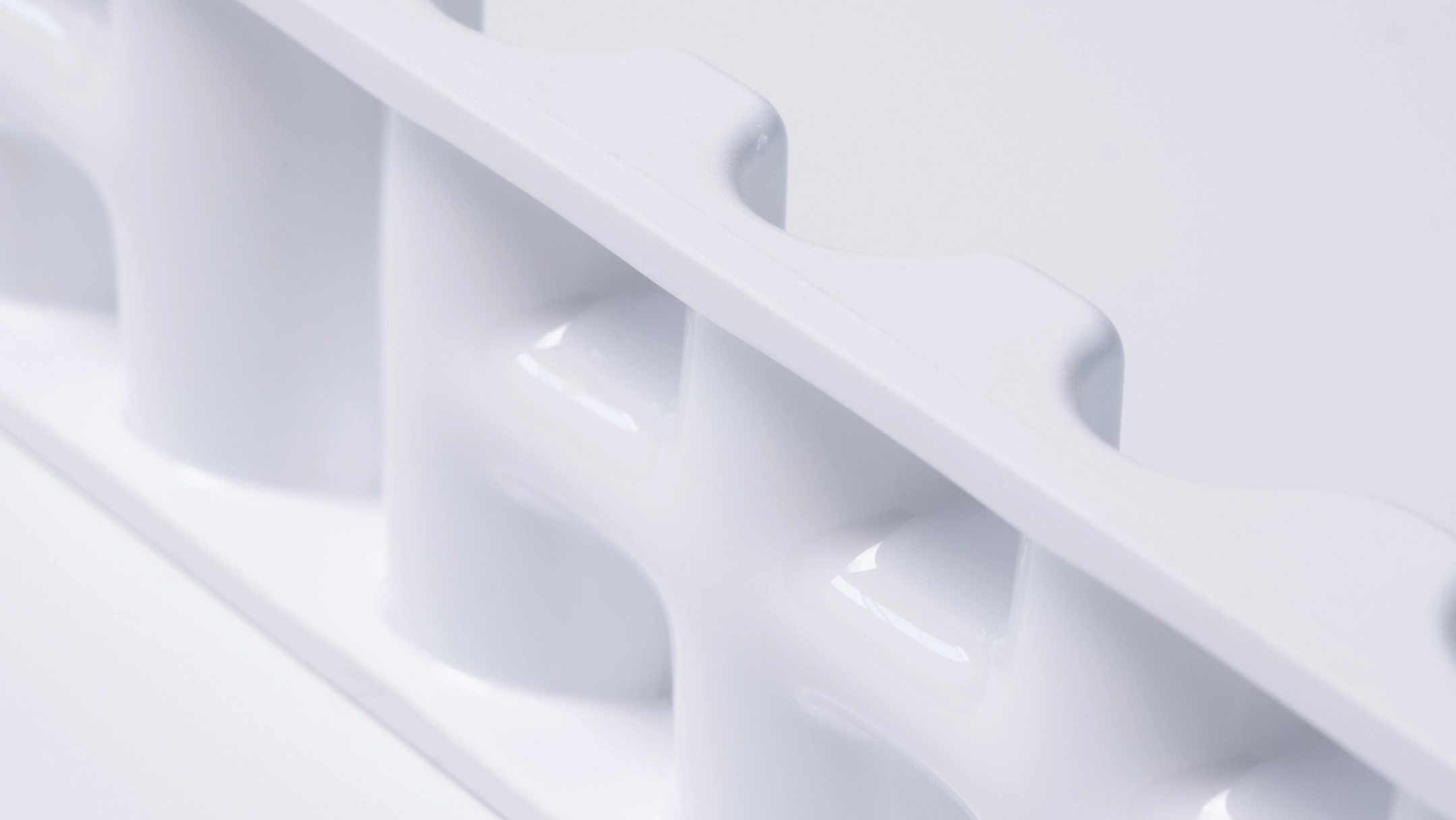
お客様の課題・リクエスト
医療業界で使用されるカバーを製作したいが、図面がなく、ポンチ絵のみがある状態でも依頼できるか?
ご提案
まず、必要な寸法や強度、ロット数をお聞きしました。図面を作成し、用途や使用環境に応じた素材選定も含めてご提案しました。反り対策や、薬品や食品に適した素材を選定し、最適な製作方法を提示しました。
結果・成果
樹脂切削や射出成形に比べ、試作から量産までのコストを抑え、納期も短縮できました。
形状確認も迅速に行い、設計、材料選定、加工方法を含めた総合的なノウハウを生かして、スムーズに製作を進めることができました。現在では、当社を通じて射出成形による大量生産のご注文をいただいております。
その他解決事例は下記よりダウンロードいただけます。
まずは、お気軽に資料請求をお試しください。